Imagine a bustling factory humming with activity, churning out products that are critical to our daily lives. But before the machinery starts its symphony of production, a crucial decision must be made: Where will this factory be located? This, my friends, is the realm of industrial location analysis, a process that goes beyond mere geographical coordinates. It’s a strategic dance of balancing factors like cost, labor, infrastructure, and even the local ecosystem to find the most advantageous spot for a thriving industrial operation.
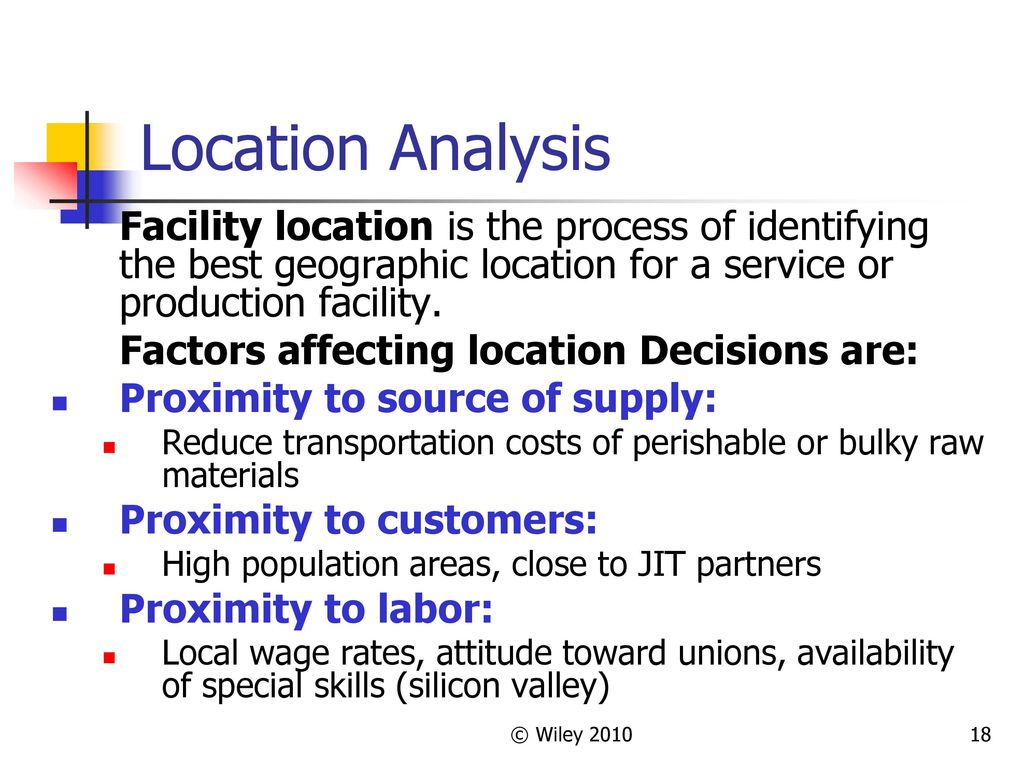
Image: slideplayer.com
Industrial location analysis is a critical element in business planning, particularly for manufacturing and logistics. It’s about maximizing efficiency, minimizing costs, and ultimately, achieving sustainable long-term growth. The right location can translate to lower production costs, greater access to raw materials and skilled labor, and even improved environmental performance. Conversely, a poorly chosen location can lead to significant logistical challenges, higher operating expenses, and even hinder a company’s ability to compete.
Factors in the Equation: A Deep Dive
Industrial Location analysis is a multi-faceted process, and that’s where the fun (and complexity) come in. Here’s where we break down the key elements that shape the decision:
1. Labor and Workforce
The availability of a skilled workforce is a cornerstone of industrial success. The right location needs to boast access to workers with the necessary skills, experience, and training. The cost of labor is equally important, influencing operational costs and competitiveness. A good location analyst will consider:
- Skillset availability: Does the location have a workforce with the specialized skills needed for the industry, such as welding, assembly, or software development?
- Labor costs: Are wages and employee benefits competitive compared to other regions? How does the cost of living compare?
- Union presence: Is the location unionized, and how might that impact labor relations and costs?
- Training opportunities: Does the area have accessible training programs, universities, or technical colleges to develop a highly skilled workforce?
2. Infrastructure and Logistics
Picture this: you’ve found the perfect workforce, but your factory is miles away from transportation hubs, critical resources, or essential infrastructure. This is where the importance of robust infrastructure becomes clear. Industrial location analysis takes into account:
- Transportation networks: Is the location well-connected by road, rail, air, and sea? Accessibility to major highways, ports, and airports is key for smooth logistics and distribution.
- Energy infrastructure: Does the area have reliable and affordable access to electricity, natural gas, or other energy sources needed for production? Does the location support renewable energy options?
- Telecommunications: Are there reliable broadband networks and sufficient telecommunications infrastructure to support data-intensive operations and collaboration?
- Water and sanitation: Does the location have access to clean water and a robust sewage system to meet the industry’s needs, especially in manufacturing and resource extraction?

Image: www.coursehero.com
3. Costs and Incentives
The bottom line: Every business aims to maximize profitability. An industrial location analysis carefully evaluates costs and potential incentives to find the most cost-effective setting. Considerations include:
- Land and property costs: Are land prices and property taxes reasonable, and are there suitable industrial sites available?
- Taxation: Do local and state governments offer tax breaks, incentives, or partnerships that can reduce the cost of doing business?
- Operating costs: How do factors like energy costs, insurance, and environmental regulations compare to other locations?
- Transportation costs: Analyze the cost of shipping raw materials, finished products, and goods within the region and internationally.
4. Environmental and Regulatory Considerations
Sustainability and responsible practices are increasingly vital for businesses. Industrial location analysis now carefully assesses environmental factors and local regulations:
- Environmental impact: How does the location impact air and water quality, and what are the potential environmental risks? Is there potential for disruption to local ecosystems?
- Environmental regulations: What are the local environmental regulations, and are they strict or lenient compared to other locations?
- Waste disposal: Does the location have adequate waste management facilities and infrastructure to support industrial operations? Are there regulations that govern waste disposal?
- Renewable energy: Does the local environment and regulations support the use of renewable energy sources such as solar or wind power?
5. Market Access and Proximity to Customers
It’s not just about production; it’s about getting products to market efficiently. Industrial location analysis considers the proximity to customers and markets, as well as the location’s role in the global supply chain:
- Customer base: Is the location close to key customer segments and markets? A nearness to major cities or distribution channels can be advantageous.
- Supply chain integration: How does the location fit into the global supply chain? Is it close to key suppliers, ports, or transportation hubs for smooth sourcing and distribution?
- Market trends: Is the location within a growing market or industry cluster? This can enhance innovation and attract talent.
- Competition: What is the competitive landscape in the area, and how does the location’s competitive environment compare to other potential sites?
The Tools of the Trade: Technology in Location Analysis
Gone are the days of manual map analysis and guesswork. Today, industrial location analysis leverages powerful tools and data to make informed decisions. Here are some key technologies used in this field:
- Geographic Information Systems (GIS): GIS software allows analysts to visualize and analyze spatial data, such as demographics, infrastructure, and environmental factors, to identify ideal locations.
- Big Data Analytics: Analyzing large datasets on factors like supply chains, market trends, and competitor locations can reveal insights and patterns that inform location decisions.
- Modeling and Simulation: Using software to simulate different location scenarios helps analysts assess the potential impact of various factors, like transportation costs or environmental risks, before committing to a location.
- Location-Based Services (LBS): Apps and platforms that use location data, such as GPS tracking, can provide insights into real-time traffic patterns, resource availability, and potential disruptions.
The Future of Industrial Location Analysis: Trends and Insights
The world of industrial location analysis is constantly evolving, driven by technological advancements, changing economic landscapes, and a growing emphasis on sustainability. Here are some emerging trends that are shaping the industry:
- Rise of Reshoring and Nearshoring: As global supply chains face disruptions and companies prioritize resilience, many are considering bringing manufacturing closer to home or to nearby regions. This trend is creating opportunities for economic development in locations that were previously overlooked.
- Focus on Sustainability and Green Practices: Businesses are increasingly prioritizing environmentally responsible practices, leading to greater emphasis on factors like access to renewable energy, waste management infrastructure, and compliance with environmental regulations. Locations that offer sustainability benefits are becoming more attractive.
- Integration with Smart City Technology: Cities are increasingly adopting smart technologies like data analytics, sensors, and connected infrastructure. This creates opportunities for industrial operations to leverage these technologies for improved efficiency, resource management, and communication.
- Digitalization and Automation: Automation and digitalization are transforming manufacturing processes, and this trend is influencing location decisions. Companies are looking for locations with a highly skilled workforce and infrastructure that supports Industry 4.0 technologies.
Industrial Location Analysis Typically Attempts To
Conclusion: Finding the Sweet Spot
Industrial location analysis is a dynamic field that requires a deep understanding of the economic, social, environmental, and technological factors that influence business success. By carefully weighing the pros and cons of potential locations, companies can make informed decisions that unlock long-term growth, efficiency, and sustainability. As the world continues to evolve, the importance of industrial location analysis will only grow, making it a critical skill for anyone involved in business planning, economic development, or the future of industrial operations.